皆さんこんにちは。KINKI KNIGHTSのラーメンおじさんです。 この記事はKINKI KNIGHTSアドベントカレンダーの8日目の記事になっています。 アドベントカレンダーが始まってから一週間がたちましたが、誰も記事を落とすことなくここまで走り抜けています。 すごすぎてびっくりです。
先日CoREのストライダーの加工でJLCPCBのCNCサービスを利用しましたので、使い勝手やノウハウをご紹介出来ればと思います。
CNCサービスの選定
KINKI KNIGHTSではメンバー宅にCNCや3Dプリンターがあり、加工にはそれらを利用しています。 また、旋盤やフライスはそれらの設備を利用できるメンバーにお願いすることもあります。 軸物加工の得意なメンバーが少ないのと、加工リソース節約を理由に、ストライダーの軸パーツを外注することにしました。
個人で使用できる手軽な金属加工の外注サービスとしてはMisumiのmevyと、JLCPCBのCNCサービス、PCBWayのCNCサービスといったところでしょうか?
今回は3種類のパーツを発注したのですが、例として下記のような軸パーツを見ていきましょう。
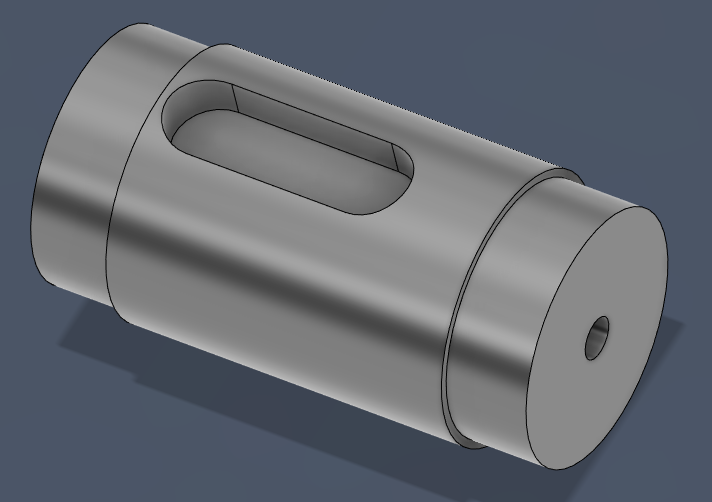
このパーツは、Φ16の軸の左右にベアリングが嵌るΦ15の段がついています。 また、軸中央に幅5mmのキー溝が設けられています。 軸の両端はM3ねじですが、コストカットのためΦ2.5の穴としネジ切りは自分で行うものとします。 材質はアルミで2000番台を考えていましたが、最終的に安価な6000番台を選択しました。
各サービスで発注個数に応じて値段が異なりますが、今回は2個で見積を取りました。 納期は1週間程度(5営業日)を基準としました。(Mevyのみ8日を選択)
サービス | 価格(2個分) | 備考 |
---|---|---|
Mevy | ¥9,308 | 公差・キー規格を指定できた |
JLCPCB | $36.19 | 公差は±0.05mmまでしか指定できない |
PCB Way | $67.71 | 公差を±0.02mmまで指定できる。(図面指示で割と聞いてもらえそう) |
見積を一目見てわかる通り、JLCPCBが最も安価です。 ただ、精度のいる加工等が必要ならMevyを使った方がよさそうです。
Mevy
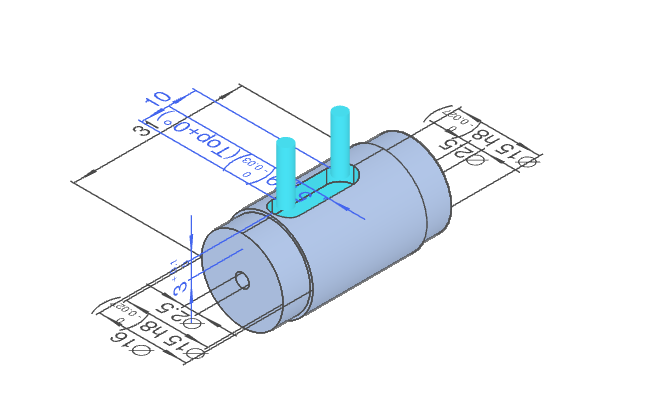
MevyはStepファイルをアップロードすると、自動で形状解析が実行されモデルが表示されます。
各段やキー、穴等についてかなり細かく公差や規格を設定することができました。
また、加工時に破綻しそうな形状を検出してくれて確認を取ってくれる等、かなり細かい品質管理がなされているイメージでした。
材質や焼き入れ等の後処理も選択肢が豊富で、痒いところに手が届くサービスだと感じました。 設定も難しくなく、公差についてなんとなく知っているという程度の知識でも問題なく利用できるかと思います。
基本的には加工条件や精度を設定することで自動で見積を算出してくれます。 まれに、特殊形状の場合は担当者による見積もりになることもあるようです。
JLCPCB
見積画面はかなりシンプルな作りで、必要最小限の項目という感じで使いやすいです。
こちらも、Stepファイルをアップロードすることで自動見積もりが可能です。
金属系の材質は銅とアルミのみで、それぞれ選択肢が豊富とは言えません。 焼き入れ等の後処理はありませんが表面仕上げ処理が選択でき、バフやビーズブラストをかなり手軽に選択できるほか、 シルクスクリーン印刷やレーザーマーキングにも対応しています。
公差は最少で±0.05mmまでしか設定できません。
±0.05mmを指定する場合は、公差指定用の図面PDFを求められます。
PCB Way
基本的にはJLC PCBと同じような操作感でした。 初手でモデルを放り込んだときの自動見積もりが高かったためあまり深堀していません。
JLC PCBを使ってみる
見積もりの結果、価格と精度のバランスを見てJLC PCBを利用することに決めました。 JLC PCBの利用は次のような流れになります。
- Webサイト上にファイルをアップロードして各種設定を行い、見積・発注ボタンを押す。
- JLC PCBのエンジニアからメールにてレビューが届く。
- レビューで修正要望があった場合はメールでやり取りする。
- レビューが通ったら、JLC PCBのサイトから支払い方法を設定して決済し加工を開始してもらう。
- 1週間程度待つ
特に注意しなければいけないのは、レビューの修正要望がJLC PCBに登録しているメール宛にくることです。 メールを確認しておらず2日程度タイムロスを発生させてしまいました。
表面仕上げ
今回は使用しませんでしたが、表面仕上げについて軽く紹介しておきます。
表面仕上げの選択肢はかなり多く用意されており、見た目重視のパーツならこれらを選択するのもかなりありです。 今回のパーツで興味本位でアルマイトの見積もりを取ってみましたが、納期が+1日、価格が2個で$2程度上乗せされただけでした。
特にアルマイト加工は各色の選択の他にマット仕上げ、光沢仕上げを選ぶことができ、かなりこだわれそうです。 自分はアルマイト加工されたパーツの発色が結構好きなので、機会があれば利用してみたいですね。
公差のやりくり
公差指定の幅の狭さはこのサービスを利用するうえで少し課題です。 軸ものパーツは、大抵ベアリングやプーリを組み付けることから、「はめあい公差」と呼ばれる精度での加工が必要になります。 これは軸の場合、指定したサイズよりも小さい範囲での誤差ということになります。
Meviyや世間一般の加工屋さんに依頼するときはh7やh8という表記で公差を指定します。 これはサイズ(基準寸法)にもよりますが、ロボコンで使用するパーツサイズだと大体図面やCADの寸法ピッタリから-0.03mmくらいまでの幅に加工時の誤差を収めるということです。
CADや図面で指定した寸法よりも大きくなってしまうと、ベアリング等に軸を圧入することになってしまい、場合によってはベアリングが変形してしまう恐れもあります。
困ったことに、JLC PCBでははめあい公差が指定できません。 最小精度でも±0.05mmの誤差までしか保証されないため工夫が必要です。 発注時に図面のPDFを添付することができるので、無理やりはめあい公差を指定してみたところレビューで怒られました。(当たり前ですね。)
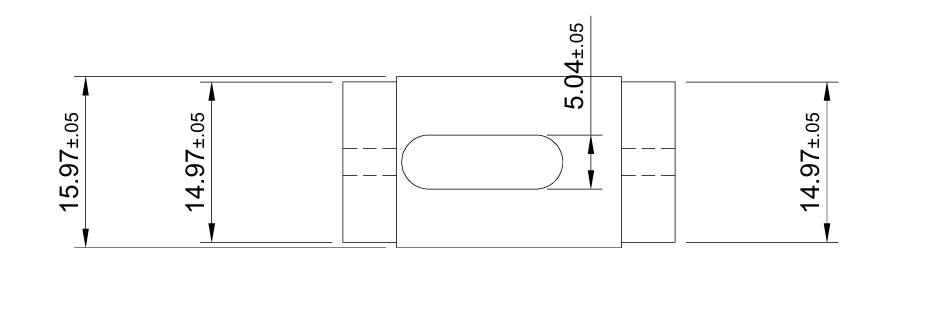
苦肉の策として、上記のような寸法指定とすることにしました。 CADのモデルの寸法自体を0.03mmずらしています。
例えば、Φ16mmの箇所はΦ15.97mm、Φ15mmの箇所はΦ14.97mmといった具合です。 本当は0.05mmずらすのが安全なのですが、加工時の寸法が小さくなると組み上げた際の軸のガタつきが大きくなります。
そのため、加工誤差が正規分布的に中央に寄ってくれることを願いながら0.03mmのずれでCADを設計しました。 最悪0.02mmくらいであればやすれば何とかなります。
結果的にこのパーツではない長さ80mm程度の軸で一部やすりがけが発生しましたが、ほとんどの箇所で想定内の加工誤差に落ち着いてくれました。
複数部品の組み合わせ
※この手法は自己責任でお願いします。
JLC PCBでは、部品個数と大まかな大きさに対して値段が算出されます。 ただ、大きさが二倍になったからと言って値段も二倍になるわけではなく、あまり値段が変わらない場合もあります。
基板を発注したことのある人なら「面付け」という手法をご存じの方もいるのではないでしょうか? 一つの基板データに複数種類の基板を並べて、Vカット等で簡単に手で分離できるようにすることで、 一枚分の製造コストで複数の基板を製造できる手法の事です。(基板にわかなので間違っていたらごめんなさい)
CNCサービスでも、あわよくばこのような手法でコスト削減できないかと思い、下記のようなモデルを作ってみました。
真ん中でポキッと折ると2パーツになります。あさましいですね。
結論から申し上げると、レビューで怒られました。
「加工時に折れてしまうのでΦ3以上に修正してください」とのことでした。
修正の結果このようになりました。
端面は気にしないパーツですので、届いたらコンターでぶった切る予定です。
最後に
今回はJLC PCBのCNCサービスを利用方法や公差指定のノウハウを紹介しました。 Mevyに比べると若干痒いところに手が届かない感はありますが、納期と価格が圧倒的に勝利しています。 また、発注側の少しの工夫で公差等の問題も案外クリアできます。
実際に届いてみたパーツの感想ですが、クオリティが高く申し分ない出来でした。 これからもJLC PCBを愛用していこうと思います。 ちなみに、Mevyではエラーの出ていた壁の薄い加工箇所ですが、危なげなく綺麗に仕上がっていました。
最後までお読みいただきありがとうございました。
明日は、ぱぁさんの技育展の記事になります!お楽しみに!!
お知らせ
KINKI KNIGHTSでクラウドファンディングを開始しました。
皆様の応援をよろしくお願いします!
【クラファン決定!】
— KINKI KNIGHTS (@Kinki_knights) November 30, 2024
KINKI KNIGHTSではチーム拡大と目標達成に向け、クラウドファンディングを始めます!!
目標金額の達成に向け、皆様の御支援をいただければと思います!
よろしくお願いします!#KINKIKNIGHTS#CoREjp#レスコン2025https://t.co/nnb3X8cA20